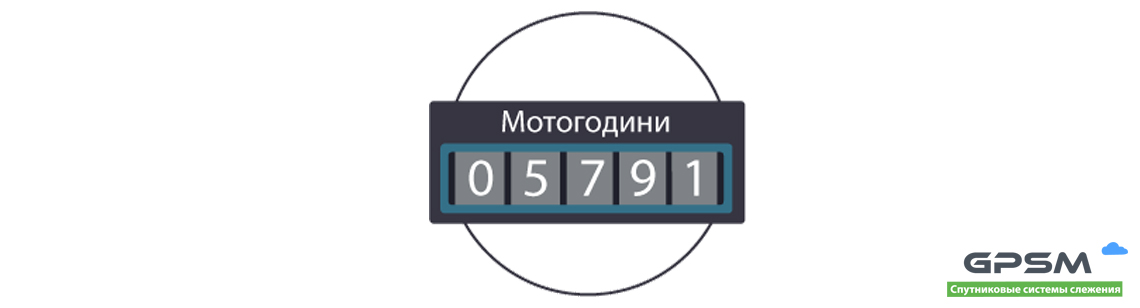
How to Monitor Hours and Engine Runtime with GPSM?
This article will focus on monitoring engine operating time, units and engine hours using the GPSM Pro GPS tracker.
What is the engine running time used for:
- To know when the work was done;
- Determine the modes in which the equipment worked;
- Write off fuel by engine hours;
- Avoid tampering with fuel. There are several ways to monitor engine run time.
There are several ways to control the engine running time:
Monitoring the engine running time by rpm:
This method is more difficult to connect. The tracker counts the pulses corresponding to the engine speed. For RPM control, the GPSM Pro tracker has a pulse input that counts the pulse frequency. To control the engine speed, the pulse input is connected to the vehicle's electric generator. Alternator RPM is correlated with engine RPM. The sensor is calibrated as follows: The number of pulses of the generator at idle turns is checked, it is checked against the revolutions of the tachometer, the number of pulses at 1000, 1500, 2000, etc. is recorded in the same way. In the future, the system automatically approximates and recalculates the generator speed to the engine speed.
The technology allows you to: Obtain information about real engine hours, control engine overspeed, work for engine wear. To obtain information about real operating hours, the GPSM system indicates a formula with which the engine operating time is calculated, taking into account the engine speed:
1 minute of operation at 2000 rpm corresponds to 1.5 minutes of engine hours
1 minute at 1500 rpm - corresponds
1 minute of engine hours 1 minute at 1000 rpm corresponds to 2/3 minute of engine hours
1 minute of operation at 500 rpm corresponds to 20 seconds of engine hours
Cons: installation takes more time compared to “ignition lock control”, GPS tracker with frequency input is required.
Pros: The most accurate method for determining engine performance. In the field, it is almost impossible to imitate the operation of the engine, wind up the engine hours. An accurate way to determine the running time (astronomical time) of the engine. Method for calculating engine operating hours for fuel write-off.
Engine condition monitoring:
vehicle ignition on or off. This method is the easiest in terms of installation, it is supported by almost all vehicle trackers. The tracker has a voltage-activated trigger input. The tracker input is a voltmeter. When the specified voltage appears, for example, 12 or 24 volts, the input is activated. The system receives information about turning on the ignition when voltage appears.
Pros: ease of installation, clarity.
Cons: on trucks, after disconnecting the mass, a “plus” may appear at the tracker input, and the system will consider that the engine is running. The driver can apply a plus to the tracker input and the system will begin to count the extra engine running time. The second special case, when the input is connected to the ignition switch circuit, the input will be activated when the ignition switch is turned, but the engine will not start.
When the ignition is controlled using a trigger input, we receive information about the state of the engine online. Also, information is saved about the astronomical hours of the engine or other units.
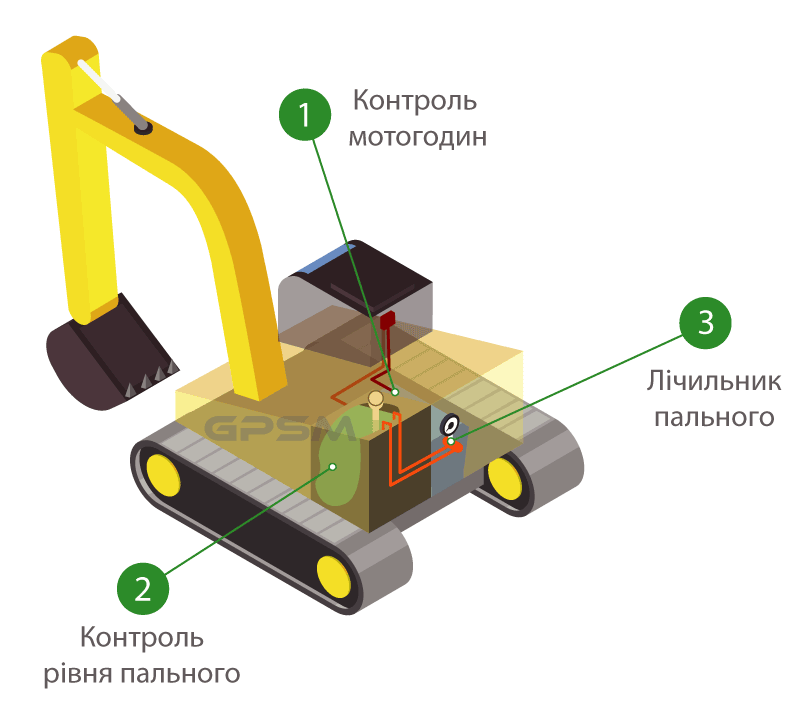
Monitoring of engine hours using fuel flow meters:
This function is built into the fuel flow meters of two Belarusian manufacturers Mechatronica, Technoton and one European manufacturer - Atomic Engineering. There is no built-in function for monitoring the engine running time in Chinese and Swiss flow meters. But we can calculate it using GPSM software by estimating the fuel flow rate.
Flow meters do not determine the engine speed, therefore, they cannot calculate engine hours. But according to manufacturers, they calculate the engine operating time and determine the engine operating modes (based on the rate of fuel consumption). We tested the engine runtime monitoring functions of the specified manufacturers and obtained the following data:
Technoton flowmeters gave an error of 5% in engine operation time.
- Mechatronic flowmeters had an error of the engine running time of about 30%. At each stop, the meter added 15 minutes to the engine running time. Thus, the error can be even greater if the frequency of starts and stops is more frequent. If the frequency of starting and stopping the engine is less, then the error will be less.
- Atomic flow meters showed the best results.
- The error in calculating the engine running time did not exceed 1%. We have tested this feature on both single and dual chamber meters.
Conclusion: if you control the engine running time using the flow meter, the Atomic flow sensors work most accurately. Also, the time can be calculated based on the fuel flow rate directly in the software itself.
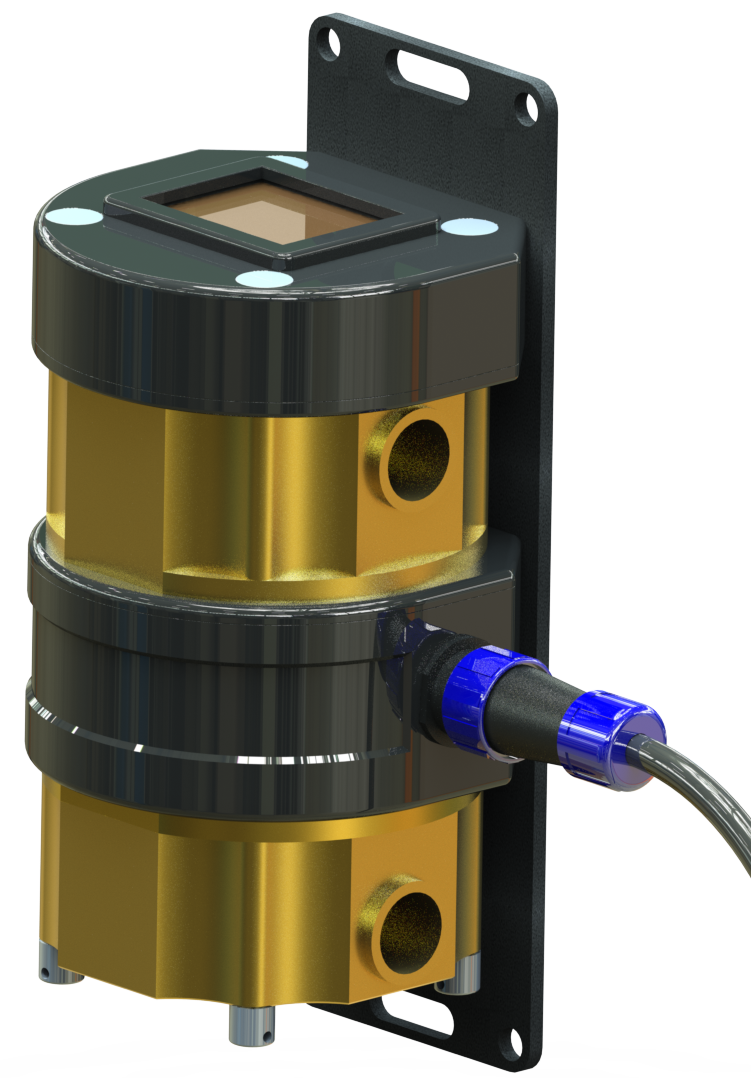
Monitoring of engine hours via CAN bus:
Today, the most popular models are:
1. OBD-2 trackers, which are installed directly into the diagnostic socket of cars / trucks. A large amount of data is read, including fuel consumption, trip time, accelerator pedal pressure, brakes, etc.
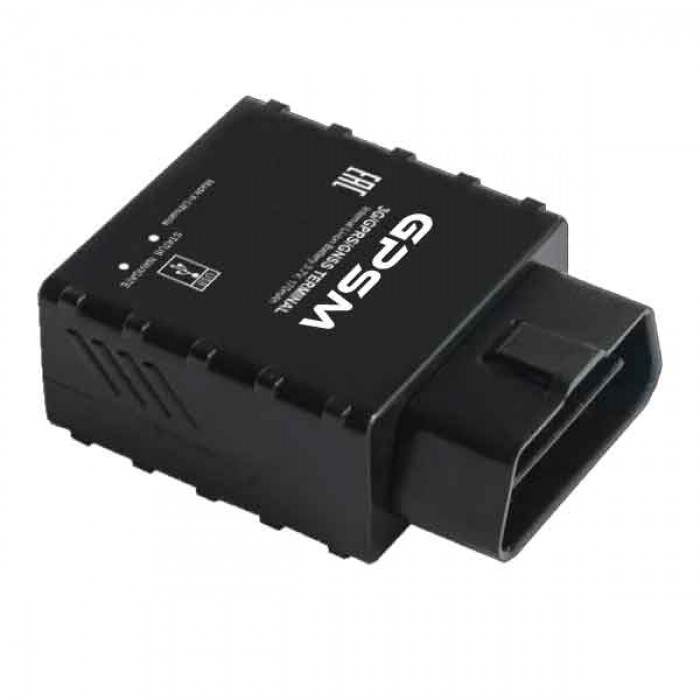
2. CAN-logger is a compact device that connects to the vehicle's CAN-bus, decrypts the parameters using the RS-232 interface and connects to the GPS tracker. CAN-logger decodes significantly more parameters than standard OBD2 trackers.
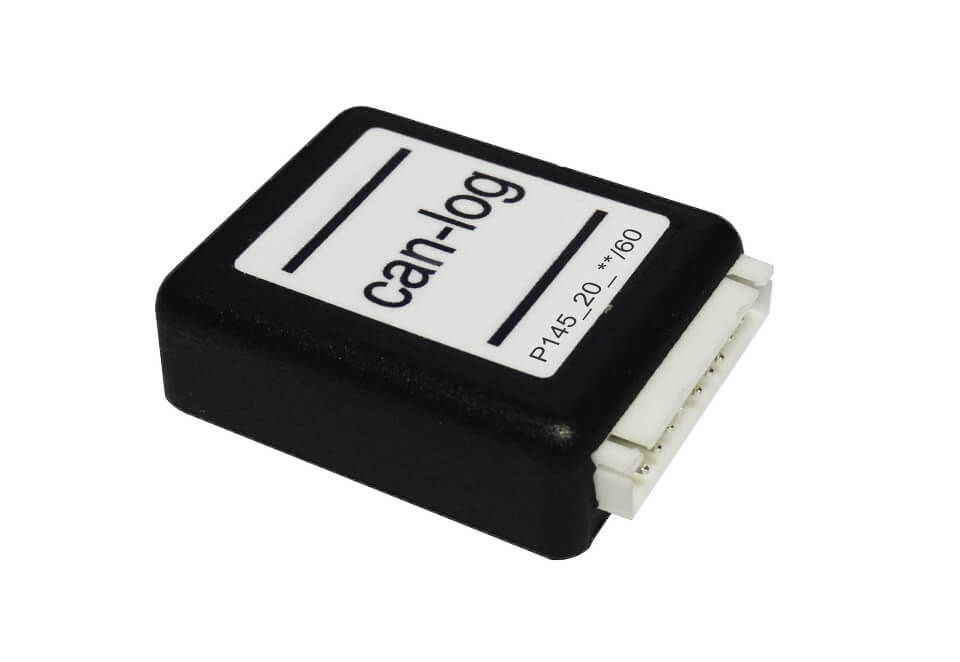
3. GPS tracker GPSM U1 CAN - this tracker has a CAN interface that reads absolutely all known parameters that are in the vehicle's CAN bus.
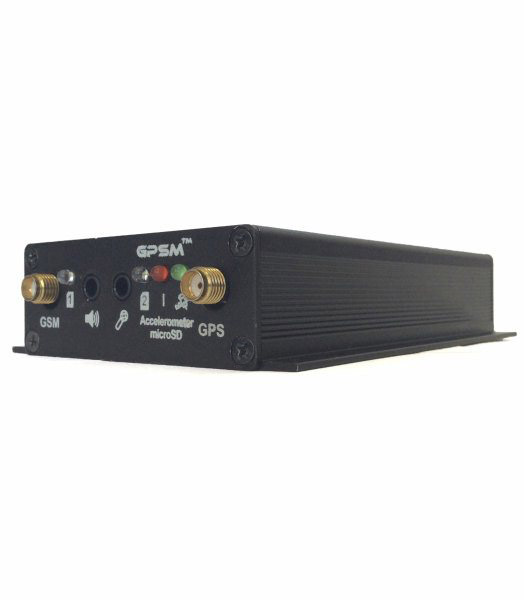
Also, there are other ways to control the engine hours, for example, by reading pulses from the engine injectors, connecting additional sensors to control the speed, are rarely used.
Consultation
GPSM specialists are ready to help you choose the best solution for your business. To order a turnkey installation, call 044 362 29 56, 097 696 84 07 or send a request to info@gpsm.ua. We will promptly call you back and send you a letter with a commercial offer.
Our staff is represented by real professionals with extensive experience. We have successfully implemented a comprehensive monitoring system on vehicles such as trucks, public transport, agricultural, construction, road equipment and others.
Take a modern approach to improve the efficiency and profit of your business! The GPS vehicle monitoring complex is a reliable method for optimizing the operation of a vehicle fleet and reducing the cost of its maintenance by 25-40%. Investments in the implementation of a transport control system pay off within a few months. Cut your fuel and spare parts costs today!
Our Instagram: https://www.instagram.com/gpsm.ua/
Our Facebook: https://www.facebook.com/gpsm.ua/
Comments
Thanks!
Your comment has been sent.
Be the first to leave a comment here!